Meat Suppliers Implement Additional Safety Measures
Like retail counterparts, worker safety is paramount. During the coronavirus pandemic, plant worker safety is paramount, similar to their retail counterparts.
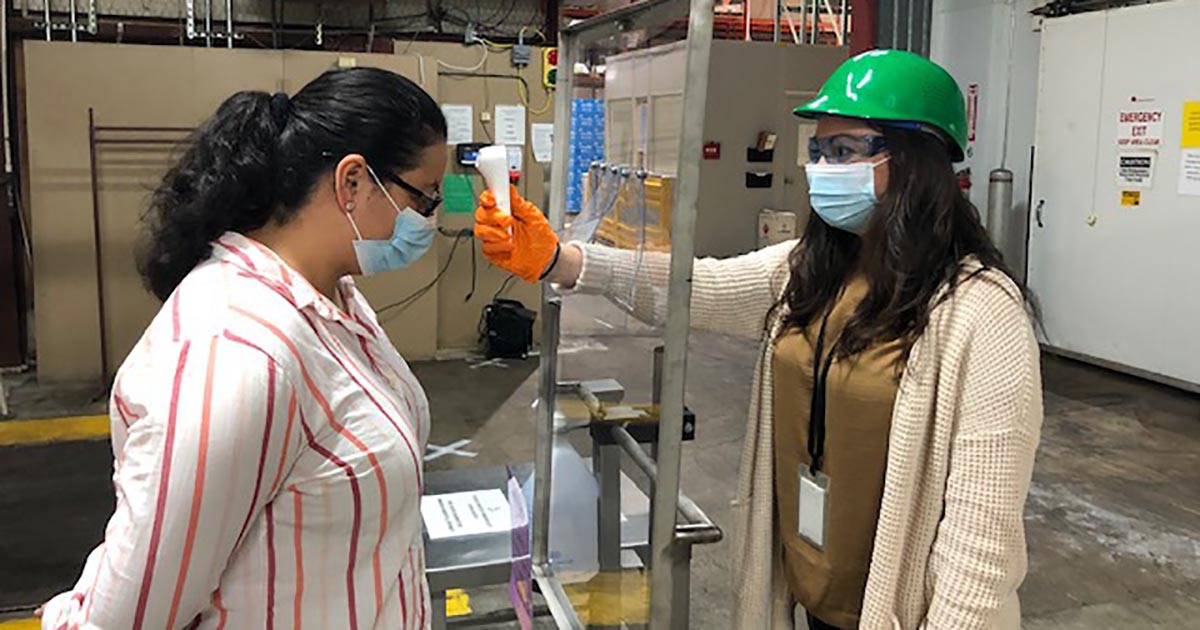
Retailers are not the only one grappling with protocol when a worker comes down with COVID-19. Manufacturers throughout the supply chain are dealing with the same issues of worker safety and figuring out how to keep workers healthy.
In the past few weeks, several meat production facilities have had to close down processing due to COVID-19 outbreaks among workers. JBS has had to close its beef-processing plant in Souderton, Pa., for two weeks due to workers testing positive, while more workers have tested positive in its Greeley, Colo., facility, causing a walkout by employees earlier this week. Empire Kosher is expected to reopen its chicken processing plant on April 13 after two employees tested positive for COVID-19, while National Beef Packing temporarily closed its Tama, Iowa, facility.
Tyson Foods had to temporarily close its Columbus Junction, Iowa, plant after 24 workers tested positive, which has led the company to implement new safety and sanitation procedures, similar to what its retail counterparts have had to do. The company is taking the temperature of every employee before they start their shift and has even installed infrared temperature scanners that are quicker and more precise than temporal thermometers. At the facilities with the infrared scanners, employees simply walk through a scanner similar to a metal detector at airports.
“We’re also coordinating with federal agencies to emphasize the need for personal protective equipment to support our team members as we remain open. We’re working to secure an adequate supply of protective face coverings for production workers and have implemented interim protocols for temporary protective coverings while observing food safety,” the company said in a statement. “We continue to explore and implement additional ways to promote more social distancing in our plants. This includes erecting dividers between workstations or increasing the space between workers on the production floor, which can involve slowing production lines. We’re also creating more room in nonproduction areas. For example, at some locations, we’ve set up tents to create outdoor break rooms. …While these are challenging times, we remain committed to protecting our people while continuing to meet the needs of our customers and consumers across America.”
Photograph courtesy of Perdue Farms
Salisbury, Md.-based Perdue Farms also is implementing additional safety measures. “As the COVID-19 crisis continues to evolve, we’ve enacted numerous proactive measures to protect our associates during this uncharted time,” said Perdue Farms CEO Randy Day. “For example, at our plants, we are practicing social distancing not only in common areas, such as break rooms and cafeterias, but also on the production lines where possible. Where social distancing isn’t possible, we are rolling out temporary installations of dividers between our associates on production lines.”
The partitions, which were designed and made by members of Perdue’s engineering, maintenance and operations teams, are easily customized to fit differing functions throughout the plant and the stainless elements are welded vs. bolted to minimize potential pathogen harborage points. Made using either Plexiglas or stretched trash bags, the dividers will be cleaned or replaced, respectively, between every shift.
Additional measures include infrared non-contact temperature devices to take the temperature of each team member before shift, as well as the handing out of disposable masks. In addition to incremental safety precautions in the facilities, Perdue has increased compensation for associates and added flexibility to the leave policies.
Since the pandemic caused many of associates to cancel vacation or personal time off (PTO), Perdue has temporarily removed the PTO accrual maximum for all associates until June 1. This will allow associates to continue accruing PTO weekly/biweekly past the maximum amount, and they will have until June 1, 2021, to use the days over their PTO maximum. Other changes include providing all hourly associates a $1-per-hour pay raise and all Piece Rate associates (such as Perdue truck drivers) a $40-per-week pay increase. These temporary increases will be in effect March 23 to May 10, 2020.
“Our primary focus is the health of our people. As a 100-year-old company, we have always known our associates are front-line heroes in America’s food supply chain. As they remain dedicated to their essential roles to help keep our nation fed, we remain committed to supporting and protecting them,” Day said. “As we navigate the challenges posed by this unprecedented pandemic, we will continue to seek additional opportunities to protect and support our associates who are continuing to produce safe, high-quality food for our country.”
About the Author
You May Also Like