How Retailers Can Make Effective Energy CutsHow Retailers Can Make Effective Energy Cuts
Tweaks to reduce energy bills can add up to big savings. From LED lighting to better employee awareness, grocers can do a lot to reduce energy bills and benefit from sustainable practices.
September 3, 2019
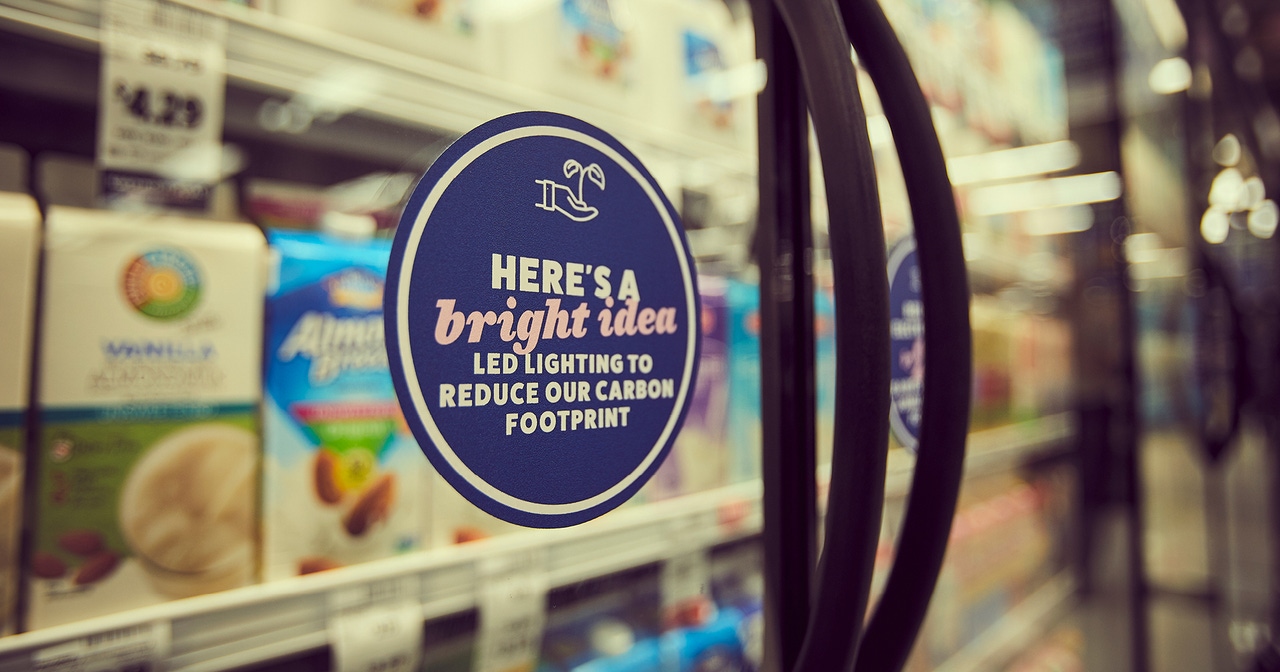
When K-VA-T’s Food City chain opens a new store in Calhoun, Ga., in November, the Abingdon, Va.-based retailer will use a number of energy-saving concepts that “are a culmination of the programs we’ve developed and implemented over the past 10 years,” says President and CEO Steven Smith.
Now that there’s more focus on the ability to save energy—and concurrently save money, while also being environmentally sound—grocery stores are making changes to their operations. These changes are typically small but have the potential to add up to big dividends for the bottom line.
The easiest way to save energy is in refrigeration doors, which can lead to a savings of about 70%, Smith says. At the soon-to-open Calhoun Food City, all coolers will have doors, except fresh meat, deli cheese and wet-rack produce. All walk-in coolers, freezers and offices will be fitted with motion sensors, ensuring the lights remain off when not in use, which leads to a huge savings because these areas require lighting only about 20% of the time.
Food City will also install only LED exterior parking lot lights, which are about 65% more energy-efficient than traditional lighting. What’s also cool about LED lighting—which will also be used for interior and case lighting, resulting in energy savings of 25% to 30%—is that it also allows the light to be projected directly onto the parking lot with less spillover.
Photograph courtesy of Food Lion
Calhoun won’t be the only store to feature these energy-saving initiatives; they’ve been implemented in several other locations, and “we’ll continue to include these concepts in our new store constructions and remodels,” Smith says.
PCC Community Markets in Seattle is also embracing more energy-efficient solutions, as evidenced by its May announcement that it will be the first grocery store to pursue Living Building Challenge Petal Certification—the world’s most rigorous green building standard. “We set high standards for the food we allow on our shelves, and we believe that our stores should be held to equally high standards,” says Brenna Davis, PCC’s VP of social and environmental responsibility. “We are reimagining how grocery stores are built: using less water and energy, designing refrigeration systems that have a reduced climate impact, utilizing building materials that protect human health.”
PCC will pursue this certification for five new stores. On the energy-saving side, it will include energy-efficient lighting, heating, ventilation, air conditioning and refrigeration equipment; and sustainable refrigeration systems that use refrigerants with a lower climate impact.
Replace and Retrofit
SpartanNash’s Family Fare stores has reopened 18 stores in western Michigan after an $18.3 million rebranding that included energy-saving initiatives, including for refrigerated cases and more upgraded LED lighting in 15 of the stores, which will result in an 8% annual reduction in energy consumption per store. “We replaced or retrofitted more than 320 feet of cases in our produce, frozen food and dairy departments,” says Tom Swanson, SVP and general manager of corporate retail at SpartanNash, who points out that the “new cases are 20% more energy-efficient.”
Overall, Swanson says the upgrades will result in annual savings of $187,500, though the return on investment is longer: Lighting has a three-year payback and the refrigerated cases take about eight years. An added side benefit: The stores are warmer, encouraging customers to shop longer. “We estimate the air surrounding the glass door cases will be approximately 16 degrees warmer,” he says.
Food Lion is following similar initiatives. In April the Salisbury, N.C.-based chain was awarded its 18th consecutive Energy Star award from the U.S. Environmental Protection Agency for its superior energy efficiency. Since partnering with Energy Star in 2001, Food Lion has reduced energy consumption by nearly 28%. This has included replacing fluorescent lights in frozen and refrigerated cases in nearly all stores so far, and on the sales floor—where more than 40% of the stores have been converted so far. Food Lion has also installed doors on medium-temperature cases and improved practices for refrigeration monitoring.
Whole Foods Market, Austin, Texas, is following a different route and is working to store energy with several third-party partners as it continues to explore a number of options, including rooftop PV plus storage and thermal storage technologies.
To date, Whole Foods in in Northern California has a half-dozen stores with energy storage systems, with more coming online in the next year. “The idea is to optimize how and when we use energy,” says Tristam Coffin, director of sustainability and facilities. “It’s an ever-evolving math equation.”
Employee Engagement
In 2017, Food Lion ran an internal challenge, Battle of the Buildings, pitting stores from two regions against each other to see which could save the most energy. Stores were given tips such as reminders to keep refrigerator doors closed, turning off lights in back rooms and entering timely work orders. “It created excitement and awareness across the stores about energy reduction and the importance of conservation,” says Food Lion spokesperson Emma Inman.
Forty-five Whole Foods stores in Northern California are doing something similar to engage team members in energy savings. “Our main priority was team member engagement in energy savings and care for the environment,” Coffin says.
“The aim was behavioral changes rather than technology upgrades,” he says, adding that there’s a potential energy savings of 5% to 10% in behavior change alone. He worked with Manomet, a Portland, Maine-based company that offers a Grocery Stewardship Certification (GSC) program, which has a goal of creating more engaged employees in terms of energy and resource efficiency.
As a result of GSC, Manomet estimates those 45 Whole Foods stores are saving more than $6 million, annually averaging about $133,400 per store; saving more than 18 million gallons of water; and preventing the release of more than 78,000 metric tons of greenhouse gases compared to the average grocery store.
“The focus areas of GSC are very broad, and there are easy behavioral changes that yield big results,” Coffin says. “It’s about employees being able to connect the dots on a number of levels—not just energy but product integrity and shrink and being able to reduce waste.” The best thing, he says, is “this makes team members feel like they’re part of the solution.”
Manomet’s GSC program, which is used by 19 U.S. retail chains and more than 20 independent grocers in the U.S. and Canada, was established by Peter Cooke, director of retail sustainability. “Many retailers tell me it’s too hard to engage employees, but it isn’t,” he says, and instead counters that “it’s imperative that they do so.”
In most grocery stores, Cooke says he can easily find $15,000 in savings. “It’s a lot easier to reduce costs than increase sales,” he says.
Cooke offers four easy ways engaged employees can help save a supermarket’s energy:
Make sure refrigerator air vents are not blocked. On average, stores have 20 feet of blocked air vents, which totals $36,000 of wasted energy per year.
Have employees note when gaskets around freezer doors are leaking. Employees can easily recognize this, Cooke says, but they often don’t know who to tell or even if they should report it. “If only employees knew that cost $4 a day, and for a chain with 200 stores, that can really build up.” He says the finds a faulty door 80% of the time he’s in a grocery store.
Turning off equipment at night. The biggest perpetrator of this energy suck is heated wrapping machines, he says, though kitchen hoods are also culprits.
Monitor out-of-order electronic games that are still using electricity or vending machines that are outside in cold weather climates and are barely used. All of these machines should be temporarily turned off.
To communicate this to employees, Cooke says, grocery stores need to provide employees with concrete figures on how much energy—and money—the store will save, and how much that will help the environment. “You need real reasons,” Cooke says. “Employees want to feel the contribution they have to the company they work for is of value.”
About the Author
You May Also Like